Craftsman Scroll Saw Manual
Blade Tensioning
Before you do much else with a scrollsaw, it's necessary to get the correct tension on the blade. With nearly all scrollsaws, 5' plain end blades are the type most often used. Some holders will take pin end blades, which are available in fewer types and sizes--the pin end blades do not come in extremely small sizes--than are plain end blades.
Manuals and free owners instruction pdf guides. Find the user manual and the help you need for the products you own at ManualsOnline. Owner's Manual.1/8HP, (Maximum 5' Pin End Blade Developed) 1725 S.P.M. ScROLL SAW Model No. 137.216160 CAUTION: '. ' ' Before using this Scroll Saw, read this manual and follow all its safetyRules and Operating. Instructions.
103.23440 Craftsman 24' Walking-Beam Jig Saw Operating Instructions. Scroll/Jig Saws. Over the years and information in old manuals as well as the old machines. MAKING gNTERtOR SCROLL One of the features of this saw is that it can be used to make scroll cuts on the interior of a board without breaking or cutting into the outline or perimeter of the board, WARNING. Page 18 Lubricate the arm bearings after 10 hours of use.
- Craftsman 113.236150 Scroll Saw Owners Instruction Manual Reprint Plastic Comb on Amazon.com.FREE. shipping on qualifying offers. Craftsman 113.236150 Scroll Saw Owners Instruction Manual Reprint Plastic Comb.
- Craftsman 21609 - 18 in. Scroll Saw Manuals & User Guides. User Manuals, Guides and Specifications for your Craftsman 21609 - 18 in. Database contains 1 Craftsman 21609 - 18 in. Scroll Saw Manuals (available for free online viewing or downloading in PDF): Operator's manual.
Blade tensioning on scrollsaws is even more of an art than it is on bandsaws. Getting one's nerves worked up to the point where it's possible to get past too low tensions takes time and practice, but few blades break from over-tensioning--too low tensioning allows an arch that can cause a break, and rough material handling can also snap blades. For those of us who are musically challenged, the fact that the blade hits a certain note when tensioned correctly is only a small help. Each size blade his a slightly different note. In fact, if the blade makes any musical sound when plucked or strummed, it is close enough to correct tension. You can also feel some resistance as you strum the back of the blade. That resistance, coupled with the note, will give you a reasonable start on a correctly tensioned blade. Practice. Check your cuts. Keep track of blade breakage. All are good ways to improve your tensioning skills.
Craftsman Scroll Saw Manual
Shawn wasabi marble soda download. Squaring the Blade To The Table
Squaring the scroll saw blade back-to-front is not of particular importance with a scrollsaw--if it were, the C arm type couldn't exist since it rocks the blade back and forth. For many very thin cuts, even side-to-side squareness is of far less importance than it is with almost any other stationary saw. But it really shouldn't be totally ignored: when pieces must fit together, or you're doing stack cutting, or cutting thicker stock, side-to-side squareness is important.
Most scroll saws require only that you move the table to adapt to 90º or any other angle. Just making sure that it is in square is a very simple matter, then.One other factor with scrollsaws, relating to squareness, is the insert. On new scrollsaws, the inserts fit nicely, are not chewed up, and allow you to easily square up work on the table. On older saws, the inserts can be a problem. The easiest solution is to make your own, using the original insert as a template or plan drawing. You can even use the scrollsaw to cut its own inserts, and then cut the slot, as desired. The strongest requirement here is the need to have a piece of material exactly as thick as the original insert so that the top is absolutely level with the table top.
Materials for inserts are variable: phenolic, softer aluminum alloys, tempered hardboard, solid wood, plywood, or even clear (or colored if you like that) acrylic and polycarbonate plastics work well.
Setting Up The Hold-Down And Dust Blower
Smooth cuts are what you're looking for on the scrollsaw, so using the hold-down and the sawdust blower are nearly essential to doing the work right. The hold-down, set to barely touch the work surface, helps keep the workpiece from catching a tooth on some quirky grain and jumping off line as you cut, while the sawdust blower keeps a clean line for you to follow.
Most scrollsaws come with blowers. It's a good idea to add one if yours didn't. Keep the tubing fresh, and make sure the nozzle points where you want it to…and that may vary depending on where the cut is going, though for a lot of work, aiming the blower just at the blade, pointing slightly to one side or the other seems to work best for many people.
And that about takes care of standard scrollsaw preparation. You can, over time, get into checking belt tightness, lubrication and other needs, but right now, let's go cut something.
Scrollsaw hold-downs are lightweight, as are the woods used in projects, and shouldn't impede the progress of the wood through the blade in any direction. A bare touch is all that is necessary, and all that is desirable.
Basic Speeds and Feeds
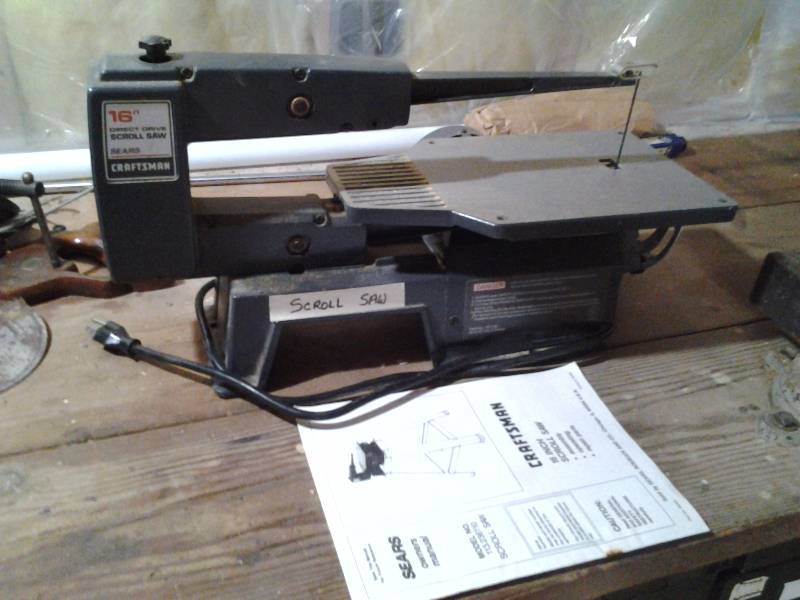
Let's figure you've got the right blade for the job to be done. It's in and ready to go, the wood is in your hand, and you're standing in front of the scroll saw. Turn it on.
Old Craftsman Scroll Saw Manual
Set the speed for the material, if this is a multi-speed or variable speed scrollsaw. The harder the material, the slower the stroke you want to use. Metals, using the correct blade, use the slowest possible speeds. Hardwoods need a slower speed than softwoods, and soft maple can take a faster speed than can hickory. Soft maple is a popular scrollsawing wood, as is tulip (yellow) poplar, basswood, butternut and similar 'soft' hardwoods.
Feed at the speed that feels right to you. Feed rate is almost entirely determined by feel, with your fingers and eyes and ears feeding back to you the information on whether or not you're moving too fast or too slow. This naturally means you're going to mess up a few pieces of wood when you first start, but practice cures that, and quickly. If you can see and hear stress on the blade, then the feed is too fast, no matter what your hands seem to say. Back off. If the blade is tensioned correctly, you'll be able to make a few over-pressure mistakes, adapting to slower feeds as you get the feel.
Holding The Work
Even though you have a hold-down in place, your hand placement is important to correct feed and the ease with which you can follow your line. You use your hands to hold the workpiece down, and, at the same time, to feed the work into the blade. The hands supplement the hold-down in keep the workpiece from rising as the blade cuts. Actual hand placement depends a lot on the size and shape of the workpiece, but whenever possible, both forefingers and the thumb of one hand are used to move the work through the blade, while keeping the cut on its line. This grip is easily modified for left and right-handed people, and also can be changed as workpiece size seriously decreases.
Other fingers need to be kept away from the cut line, more or less splayed from the hand, instead of curled back towards the palm. This helps keep them away from the blade. Again, this procedure can, and should be, modified whenever it puts the fingers in a dangerous position. Never solidify so much on one method of feed that you end up feeding that way as your finger goes into the blade. Scrollsaws are safe tools, but those little blades are sharp enough to cut sheet metal, so make certain your fingers are never in the cut.
As you feed, move a single finger at a time. Don't lift one hand and both fingers. Lift one finger, then the other, then another, as needed to follow the cut line safely.
And that's really about it. Practice. Practice a little more. It will show in your work. Scrolling isn't really difficult--the machine does the hard stuff--but practice never hurts.